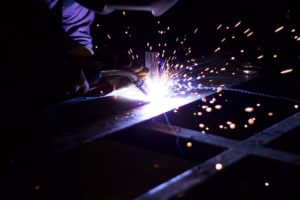
Competition is fierce in the metals industry. Steel service centers and manufacturers need to be able to respond quickly to customer needs, meeting tight price points and timelines, or risk losing work to competitors. During high volume periods or in the rush to fulfill orders, manufacturers can struggle to produce the right quantities and maintain the high quality customers demand. Control quality, quantity and profit margins by deploying a powerful business management solution, like RealSTEEL.
It can be difficult for a steel service center and manufacturer to find an enterprise resource planning (ERP) solution that fully meets operational needs. Managing inventory can be very complex, often by the very number of metal variables alone, and there are specialized calculations and processes for estimating customer orders, determining scrap, and ensuring healthy profit margins. Fighting disparate software or working with inadequate software will lead to frustration and costly mistakes. Instead, deploy an integrated business solution designed specifically for the steel and metal industry.
How ERP Technology Helps Steel Service Centers and Manufacturers Strengthen Operations
RealSTEEL is a powerful ERP solution that offers the features and functions steel service centers and manufacturers need right out-of-the-box.
- Manage your supply chain and inventory, financial and accounting procedures, production operations, sales and customer orders, and quality control procedures with greater efficiency from one solution.
- An integrated solution also makes it easier, and more productive, for your people to enter, access and share data. Data is entered only once, then can be shared within the system and across users.
- Tailored dashboards, along with business intelligence and reporting features can provide detailed insight into your business and processes.
- Armed with real-time data about business operations, you can identify new ways to streamline production and optimize resources, including manufacturing operations and personnel.
- Built-in workflows can improve the consistency of operations and you may find other ways to minimize wasteful practices and spending.
RealSTEEL also supports comprehensive testing and sampling capabilities, as well as material certification generation and tracking. Testing can validate the quality of your products and can support your ability to fulfill customer orders with the highest quality products each and every time.
RealSTEEL: All-In-One Business Management
The right technology provides a platform for steel service centers and manufacturers to strengthen operations, improve customer services and solidify their position as leaders in the industry. Contact The Wolcott Group for more information about managing quality and quantity with RealSTEEL.
By The Wolcott Group, providers of RealSTEEL, a ‘real world’ solution for the steel and metals industry.